Continuous Quality Improvement Examples in an Organization
The phrase "continuous improvement" sounds inherently optimistic — like there's the possibility that things "are always getting better." And why shouldn't they? When put in practice, the business concept of "continuous improvement" can achieve exactly that.
So, What Is Continuous Improvement?
Continuous improvement is a business management practice inspired by the Japanese concept of "Kaizen," an idiom that suggests subtle and gradual improvement achieved over time. Kaizen became the preferred modality of Japan's industrial sectors in the 50s and accounts for the rapid rise of such manufacturing juggernauts as Toyota, which rose from modest beginnings and the rubble of the second World War to become a decades-reigning auto brand. Since then, companies around the world have adopted the philosophy, modifying it to align with the needs of their particular industries.
How Does Continuous Improvement Work?
In its essence, continuous improvement is the practice of honing every aspect of your company's processes in a manner that enhances your offering's value to your customer while diminishing any activity that proves wasteful along the way.
It's important to note here that the concept of "waste," in this context, refers to those activities that are either inefficient or use resources (time, material, personnel) in a manner that isn't optimal. Continuous improvement seeks to ferret out and eliminate this waste resulting in a streamlined process that benefits both the organization and their customers.
To this end, practitioners of lean operations have adopted the continuous improvement model as a tool to optimize workflows and smash through bottlenecks in corporate cultures where one might hear "but that's how we've always done it."
Continuous improvement heralds change — not all at once — but incrementally, leveraging data and discovery along the way. It endeavors to remove cross departmental silos that prohibit communication and wasteful management issues with the ultimate goal of making an organization as productive as possible.
What Are the Four Phases of an Improvement Project?
A cornerstone of the continuous improvement is a four-part process known as the Plan Do Check Act Cycle.
The PDCA Cycle for short (and alternately, the Deming Circle, for American engineer William Deming who is credited with codifying its basic tenets), is a four-phase approach that goes as follows:
- Plan: First, an organization must recognize the opportunity to change and envision a means of achieving it.
- Do: As little green Yoda safely said, "Do or do not, there is no try." This is where the change is both made and tested.
- Check: Here, the organization reviews the test results of the change — did it work? How did it work? Analyzing the results and identifying what can be learned is paramount..
- Act: Now, it's time to take action based on what was learned in the previous step. If the change was an utter failure, being the cycle again but with a different change plan. If it worked, then implement the successful elements that were discovered and begin the process again with new possible improvements and repeat the entire process.
What's key to remember is that, like a circle, the PDCA Cycle is never-ending — it's intended to be used continuously with the goal of constantly improving your results.
Best Practices and Strategies for Process Improvement
As simple and elegant as continuous process improvement (aka process improvement) seems conceptually, bringing into your organization may be a daunting proposition to some team members.
For some, change can be uncomfortable, but then so is a wasteful organization. To help open a pathway (and people's minds) to experimenting with a new process, start with the following five precepts.
5 Ways to Begin Continuous Process Improvement
- Interrogate your organization's current standards and practices — are they contemporary with your company culture? Do they actually contribute any benefit to the customer?
- Reach out to your organization's process owners and seek their input on what may be impeding their efficiency.
- Stay open — consider how to achieve something versus negating the possibility it can be done at all.
- There is no such thing as perfection, only iterations of improvement.
- Do not let the seeking of perfection impede the implementation of a solution since no solution will be perfect.
Areas of Improvement Examples: Making Continuous Improvement Sustainable
Continuous improvement (also sometimes referred to as "continual improvement," which sometimes leads to quibbling about "continually vs continuously" — the fact is, it's the same concept), can have a direct impact on your organization's performance.
However, there's little point in implementing change if an organization reverts back to its old way of doing things. To make continuous improvement a sustainable premise in your organization, consider these three approaches.
These five areas of improvement examples will help you better understand how to implement continuous process improvement at your organization.
1. Make Improvements Manageable

So-called "moonshots" are seductive notions when making goals. When the sky's the limit why stop at the outer atmosphere, right? Well, because an unattainable goal can deplete morale and drain resources that could be better directed into more reasonable targets. Break up larger projects into more manageable chunks (which might eventually put the moon within reach).
2. Mitigate Waste

Perhaps the most evident advantage of deploying a continuous improvement practice in your organization is to reduce the amount of waste that may be occurring. Every aspect of an organization has the potential to deplete resources through antiquated or outmoded processes. Bring all hands on deck to help spot where waste may be occurring in your organization.
3. Troubleshoot in Real Time
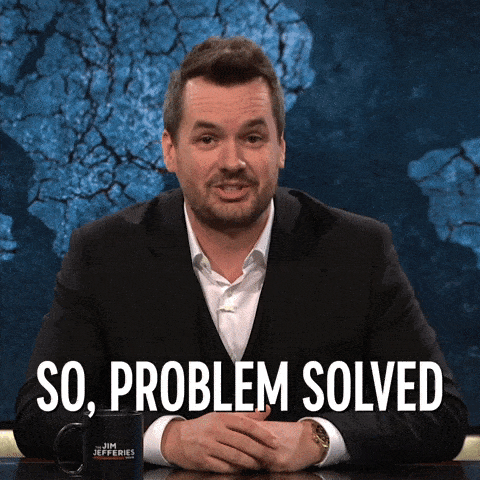
One of the most useful concepts that continuous improvement borrows from Kaizen is the encouragement to confront problems head-on in an effort to solve it faster. If an issue becomes apparent fix it immediately instead of searching for the "perfect" solution.
Waiting will inevitably cost time and valuable resources. Instead, on-the-spot troubleshooting allows production to continue while the new, improvised solution can be analyzed using continuous improvement techniques. You might find that what was first a temporary fix could lead to permanent positive changes.
4. Seek Feedback

There's an old joke that goes something like, "if suggestion boxes are emptied at all, it's usually into the trash." There are some company cultures that are reticent about soliciting feedback and input from stakeholders. Not only should your organization seek feedback, it should actively pursue conversations that evoke new ideas that could lead to new and novel opportunities for improvement.
5. Empower Employees

Empower your employees to make meaningful decisions when it comes to addressing inefficiencies and other issues that may be uncovered through a continuous improvement process. This lets them seize the opportunity to deliver a solution, your organization can not only maintain its productivity but you're fostering a culture that is intrinsically motivational.
Continuous Improvement — Why it Matters
Take a look at businesses that have integrated continuous improvement into their processes and you will surely find "areas of improvement" examples that are relevant to your own organization. Which industries can benefit from continuous improvement?
Most companies, whether they are in manufacturing or service-based industries, will find that the PDCA Cycle will yield discoveries that would otherwise elude them. The rewards can be profound — consider the following use case scenarios:
Sitting Pretty with Herman Miller
Herman Miller is the creator of perhaps the most iconic office chair in the world, the Aeron (which has the distinction of residing in the Museum of Modern Art's permanent collection). The lauded office furniture company has redefined interior design in American business culture and in 2012 it also redefined how it ran its internal operations when they adopted a continuous improvement process.
According to Fast Company, by incorporating the business philosophy, the manufacturer was able to increase its productivity by 500% and its quality by 1,000% over the previous 14 years. In a stunning representation of its newfound efficiency, the signature Aeron chair went from an 82 second assembly time on the line to a staggeringly brief 17 seconds — that's over 200 chairs an hour.
The Mayo Clinic Gets a Check Up
The nonprofit Mayo Clinic is popularly-known as a world class, life-saving hospital and research facility. According to the U.S. News & World Report, Mayo Clinic ranks as the number one hospital in the nation and offers more specialties than any of its competitors.
Despite its renowned reputation, however, the clinic knew it had an opportunity to further raise the caliber of its services by employing a continuous improvement model. How would an industrial business practice translate into a service sector that literally deals with matters of life and death?
Since their business inherently puts the customer (or in this case, the patient) first, continuous improvement was a natural. The clinic's entire care regimen was optimized to improve their patients' experience. From refining specific treatments, to the management of patient records, and even reduced waiting room times, the clinic experienced positive outcomes for their patients.
Though he didn't realize his words would apply quite aptly to a modern business practice, author Mark Twain captured the essence of continuous improvement when he remarked,
"Continuous improvement is better than delayed perfection."
Communication is key when it comes to continuous improvement. Empower your team with the best team collaboration software. Download the eBook to learn more!
Most Frequently Asked Questions
What are the most common continuous improvement processes?
A cornerstone of the continuous improvement is a four-part process known as the Plan Do Check Act Cycle.
The PDCA Cycle for short (and alternately, the Deming Circle, for American engineer William Deming who is credited with codifying its basic tenets), is a four-phase approach that goes as follows:
1. Plan
2. Do
3. Check
4. Act
What is continuous improvement?
Continuous improvement is a business management practice inspired by the Japanese concept of "Kaizen," an idiom that suggests subtle and gradual improvement achieved over time.
Source: https://www.beekeeper.io/blog/continuous-improvement/
0 Response to "Continuous Quality Improvement Examples in an Organization"
Post a Comment